ifu Hamburg, Member of iPoint Group, and Umwelttechnik BW (State Agency for Environmental Technology and Resource Efficiency in Baden-Wuerttemberg) advised different companies on material efficiency within the funding program “EFFIMA BW”. These practical case studies demonstrate the possibilities of applying Material Flow Cost Accounting (MFCA) to promote resource efficiency. The efficiency experts of ifu Hamburg helped the participating companies identify optimization potentials in their production processes through MFCA.
In this case study, ifu Hamburg’s consultants helped the fisher Group – a multinational manufacturer of fixing products – discover optimization potentials in their new production process through MFCA. By comparing different scenarios, they were able to tackle the biggest challenge in this project: identifying opportunities for increasing efficiency in the already low-loss production of two-component dowels.
Extending the potential for savings through Material Flow Cost Accounting
The high level of demand for two-component dowels (2C dowels) is sometimes difficult to meet. Production capacities must be expanded. One of the company’s goals is to increase energy efficiency throughout the company in the mid-single-digit percentage range. As the potential for savings by means of traditional methods has been largely exhausted, the applied method of material flow cost accounting (MFCA) focuses on the optimization potential of the new production facilities.
Challenge: Finding efficiency hotspots in a low-loss process
The more complex injection molding process for the 2C dowel gives it a higher energy requirement per processed material than the 1C dowel. Since no sprue is required and there is thus no planned loss, the process is already characterized by high material efficiency. Predicting the profitability of optimization measures in the overall system is nevertheless a complex task.
In order to comprehensively evaluate the potential savings of using low-loss production, energy and material consumption was systematically calculated as part of an MFCA. The plan included identifying hotspots in the production process and making them transparent. The process-oriented modeling of the value chain also enables the estimation and evaluation of potential technological optimization scenarios to increase efficiency.
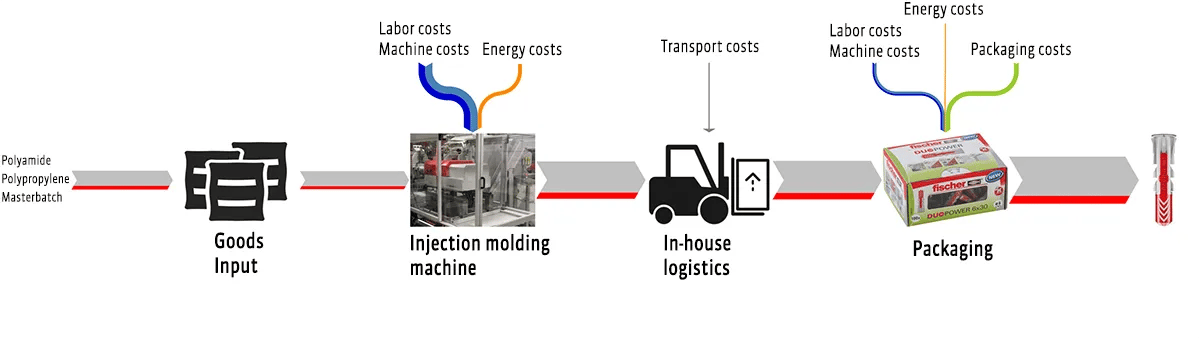
Comparing scenarios to facilitate decision-making
One of the objectives of an MFCA is to obtain a holistic understanding of the relevant processes. This is an almost automatic result of quantifying all types of consumption including the process parameters that influence them. To gain a new perspective, the status quo was modeled and validated in the process model. Modeling helps define scenarios with process variables to take into account technical interactions, thus ensuring a valid basis for making decisions about the overall process. Based on the findings about the location of process hotspots (the energy consumption in injection molding), technical measures were identified, and alternative scenarios evaluated to facilitate decision-making. Modeling also allowed the calculation of changing purchase prices and fluctuating material qualities as well as the associated effects on processability and energy consumption; the results were then evaluated in a cost-benefit analysis.
Results and revelations of the analysis
The material flow cost calculation showed that increasing the number of cavities of the new tool enhances economic efficiency despite the necessary additional investment and greater expenditure of energy – with reduced throughput time and lower energy consumption per product.
Shifting the focus from single processes towards a holistic system perspective brings up potentials even in low-loss value chains as seen in the present case. Although an MFCA focusing exclusively on losses in added value was originally thought to only suit such an analysis to a limited extent, the method (whose application was extended) provided a multitude of new findings.
The method of analysis is characterized by a structured and reliable calculation of the quantities consumed: an exclusive consideration of quantities enables a comprehensive analysis of material consumption and – based on this – the associated costs for the methodically valid evaluation of optimization alternatives. The close cooperation of all implementation partners made it possible to determine data and facts that in turn enabled an external validation of the internal balance sheets.
About the company:
The fischer Group produces dowels and construction kits as well as interior vehicle components, process consulting and electronic systems. The strong roots of the fischer family and its many employees in their native Waldachtal in the Black Forest is the basis for worldwide growth and innovative solutions: with 5,200 employees worldwide, the company earned 864 million euros in sales in 2018. fischer Befestigungssysteme is the market leader in important fields of fastening technology. fischer offers products in technical perfection for a wide range of customers, from DIYers and tradespeople to key account partners.